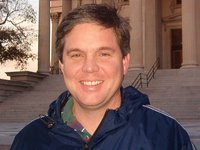
Most of the evidence is anecdotal. But what does the data say? I ran across this statistic in Saturday's paper. In the recently completed college football season, there was a total of 88,500 plays run. There are seven officials per game so there were 615,500 opportunities for officials to make mistakes (7x88,500). A total of 103 plays were overturned by replay. Interesting! Now we can make the evidence more objective.
For the non-football fan, every plan in a football game is subject to review. If a coach feels a referee made a mistake, he can ask for the play to be reviewed. The review is made by looking at the video recording of the play. If the call was obviously wrong, the decision will be changed.
So, the officials made 103 mistakes. Convert this into a conventional rate (let's use parts per million defective, PPM), and we have a rate of 167 mistakes per one million opportunities: (103/615,500)x1,000,000
How does this rate compare to your industry? In the automotive world, a 167 PPM rate doesn't keep you in business for long. The expectation is zero mistakes and the accepted performance is single digit PPM rates.
The data above came from an article written by a college football referee in defense of his profession. It was not explicitly stated but was strongly implied that 103 mistakes out of 615,500 opportunities was acceptable and does not warrant the abundance of criticism.
There are multiple definitions of quality. In it simplest form, quality is what the customer expects. The buying public wants defect free cars that will reliably operate over time. These expectations trickle down through the automotive makers to the mutliple tiers of the industry. If football fans want zero mistakes, then the bar is set. The system of officiating must respond accordingly.
2 comments:
Now, a question comes to mind. We all at some point in our lives we become both the customer and a supplier. From the customers point of view yes zero defects is the bar. What the internal defects? Does that not say a lot when your IDPPM is say at 19270 or 169 defects out of 8770? Yes these were caught within the company and did not reach the external customer, but what about all of the internal customers? This is where I think a lot of people especially in management may not see the relevence of putting in the time, effort, and money to gain control within the organization. Some would say that the IDPPM vs external DPPM has no importance but I beg to differ. Going from about 35000 IDPPM per month down to around 16000 IDPPM shows a significant improvement, and yes there is still room to improve. As it is said, we must work smarter not harder, but faster without defects.
Great points.
There is absolutely a correlation between internal PPM rates and external PPM rates.
If your internal quality is awful, your resources will be consumed with containing quality spills and trying to take corrective action. With the defect level so high, escapes to the customer are inevitable.
My experience tells me that you can't fix your internal issues if your customer is constantly breathing down your neck. So, do something to get the customer "off your back". This gives you the breathing room to take honest, corrective action.
Post a Comment